如何解决注塑中产品外观不稳定的问题
发布时间:2018-08-05 16:33来源:原创
帮助了1541人
摘要:打针成型时,温度,压力及时刻等各项工艺参数,有必要严厉依照工艺要求进行操控,尤其是每种塑件的成型周期有必要共同,不行随意改变。
打针成型时,温度,压力及时刻等各项工艺参数,有必要严厉依照工艺要求进行操控,尤其是每种塑件的成型周期有必要共同,不行随意改变。假如打针压力太低,保压时刻太短,模温太低或不均匀,料筒及喷嘴处温度太高,塑件冷却缺乏,都会导致塑件形体尺度不稳定。
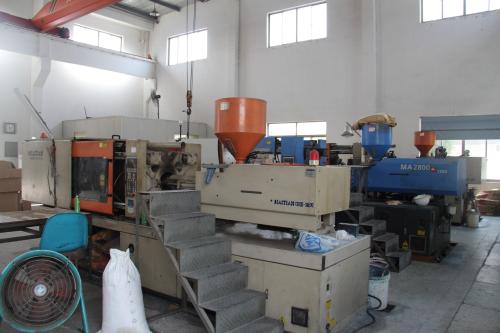
一般情况下,选用较高的打针压力和打针速度,恰当延伸充模和保压时刻,进步模温文料温,有利战胜尺度不稳定毛病。
假如塑件成型后外型尺度大于要求的尺度,应恰当下降打针压力和熔料温度,进步模具温度,缩短充模时刻,减小浇口截面积,然后进步塑件的缩短率。
若成型后塑件的尺度小于要求尺度,则应采纳与之相反的成型条件。
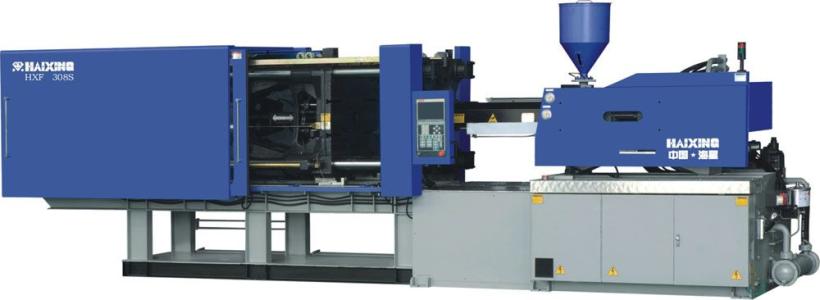
值得留意的是,环境温度的改变对塑件成型尺度的动摇也有必定的影响,应依据外部环境的改变及时调整设备和模具的工艺温度。
成型质料选用不妥
成型质料的缩短率对塑件尺度精度影响很大。假如成型设备和模具的精度很高,但成型质料的缩短率很大,则很难确保塑件的尺度精度。一般情况下,成型质料的缩短率越大,塑件的尺度精度越难确保。因而,在选用成型树脂时,有必要充沛考虑质料成型后的缩短率对塑件尺度精度的影响。关于选用的质料,其缩短率的改变规模不能大于塑件尺度精度的要求。
应留意各种树脂的缩短率差别较大,依据树脂的结晶程度进行剖析。一般,结晶型和半结晶型树脂的缩短率比非结晶型树脂大,而且缩短率改变规模也比较大,与之对应的塑件成型后发生的缩短率动摇也比较大;关于结晶型树脂,结晶度高,分子体积缩小,塑件的缩短大,树脂球晶的巨细对缩短率也有影响,球晶小,分子间的空隙小,塑件的缩短较小,而塑件的冲击强度比较高。
此外,假如成型质料的颗粒巨细不均,枯燥不良,再生料与新料混合不均匀,每批质料的功能不同,也会引起塑件成型尺度的动摇。
模具毛病
模具的结构规划及制造精度直接影响到塑件的尺度精度,在成型过程中,若模具的刚性缺乏或模腔内承受的成型压力太高,使模具发生变形,就肝形成塑件成型尺度不稳定。
假如模具的导柱与导套间的合作空隙因为制造精度差或磨损太多而超差,也会使塑件的成型尺度精度下降。很多时候实用pom原料效果会更好,更多了解pom是什么材料。
假如成型质料内有硬质填料或玻璃纤维增强资料导致模腔严峻磨损,或选用一模多腔成型时,各型腔间有差错和浇口,流道等差错及进料口平衡不良等原因发生充模不共同,也都会引起尺度动摇。
因而,在规划模具时,应规划满足的模具强度和刚性,严厉操控加工精度,模具的型腔资料应运用耐磨资料,型腔外表最好进行热处理及冷硬化处理。当塑件的尺度精度要求很高时,最好不选用一模多腔的结构方式,否则为了确保塑件的成型精度,有必要在模具上设置一系列确保模具精度的辅佐设备,导致模具的制造本钱很高。
当塑件出现偏厚差错时,往往也是模具毛病形成的。假如是在一模一腔条件下塑件壁厚发生偏厚差错,一般是因为模具的设备差错及定位不良导致模腔与型芯的相对方位偏移。此时,关于那些壁厚尺度要求很准确的塑件,不能仅靠导柱和导套来定位,有必要增设其他定位设备。
假如是在一模多腔条件下发生的偏厚差错,一般情况下,成型开始时差错较小,但接连工作后差错逐步变大,这主要是因为模腔与型芯间的差错形成的,特别是选用热流道模成型时最简单发生这种现象。对此,可在模具内设置温度差异很小的双冷却回路。假如是成型薄壁圆型容器,可选用起浮型芯,但型芯和模腔有必要同心。
此外,在制造模具时,为了便于修模,一般总是习惯于将型腔做得比要求尺度小一些,型芯做得比要求尺度大一些,留出必定的修模余量。当塑件成型孔的内径甚小于外径时,芯销应做得大一些,这是因为成型孔处塑件的缩短总是大于其它部位,而且向孔心方向缩短的。反之,若塑件成型孔的内径接近于外径时,芯销可以做得小一些。
设备毛病
假如成型设备的塑化容量缺乏,加料体系供料不稳定,螺杆的转速不稳定,中止效果异常,液压体系的止回阀失灵,温度操控体系出现热电偶烧坏,加热器断路等,都会导致塑件的成型尺度不稳定。这些毛病只需查出后可采纳针对性的措施予以扫除。
测验办法或条件不共同
假如测定塑件尺度的办法,时刻,温度不同,测定的尺度会有很大的差异。其间温度条件对测验的影响最大,这是因为塑料的热膨胀系数要比金属大工业10倍。因而,有必要选用规范规则的办法和温度条件来测定塑件的结构尺度,而且塑件有必要充沛冷却定型后才干进行丈量。一般塑件在脱形式10小时内尺度改变是很大的,24小时才根本定型。
以上关于如何解决注塑中产品外观不稳定的问题的内容对您是否有帮助?